Large Fleets: Right-Size & Manage Your Fleet
Tri-Lift is committed to delivering excellence in material handling solutions and account management.
Large fleets require the expertise and experience to optimize fleet utilization. Through fleet management, we can take the equipment ownership burden off your shoulders so you can concentrate on your business’s growth.
Tri-Lift can conduct a fleet analysis to make sure you have the most productive equipment in your fleet to meet your application needs. In addition, maintenance and auditing procedures will be put into place to maximize your ROI (Return On Investment.)
Managing a fleet whether one location or multiple locations can be a difficult and time consuming task. Tri-Lift can help optimize and manage your fleet. Our responsive team delivers personal attention by always meeting your core requirements, and through data delivering actionable items for improvement. The better the information, the more effectively you can run leaner and more cost effective operations.
Your material handling fleet is at the heart of your business.
Knowing the status of your fleet empowers your company to make real-time changes it needs to hit target metrics.
What if we can provide your company with an online portal, that can track your material handling fleet at no cost.
The fleet management dashboard provides real time information in the following areas.
- Asset List: Provides an accurate asset list that is maintained.
- Helps achieve Budget certainty: Allows you to predict & forecast maintenance budgets.
- Control Cost: Allows you to identify repairs completed and if they were needed due to misuse or application driven. You can then evaluate what is needed to eliminate these types of repairs in the future. Potentially large savings.
- Planned Maintenance Schedules: A proper planned maintenance service has shown lower cost of maintenance and safer work environment. You can know track if maintenance is being performed when due.
- Equipment Utilization: Identify trucks in your fleet being over or under-utilized. It will give you the ability to reduce fleet size or move equipment around in the facility to help average out fleet hours so to get overall fleet costs down.
- Budget equipment replacement: Allows you to identify the proper time to replace your equipment and when. Industry explains that the time to replace equipment is when the overall maintenance cost has exceeded the original purchase price. Another indicator is 10,000 hours of usage depending on application or how well-maintained unit has been serviced. Year of unit also plays a major factor on value of equipment along with a large service repairs needed.
- Fleet Safety: Properly maintained fleet and away to tract equipment, results into better uptime, performance, safer equipment and return on investment
This and a telematics solution provide customer with a complete visibility of one of his most important part of their operation.
Please contact us for additional information and free facility assessment to show how our fleet management software can work for you.
Forklift & Aerial Lift Rentals
We’ve got the forklifts and aerial equipment to raise your productivity!
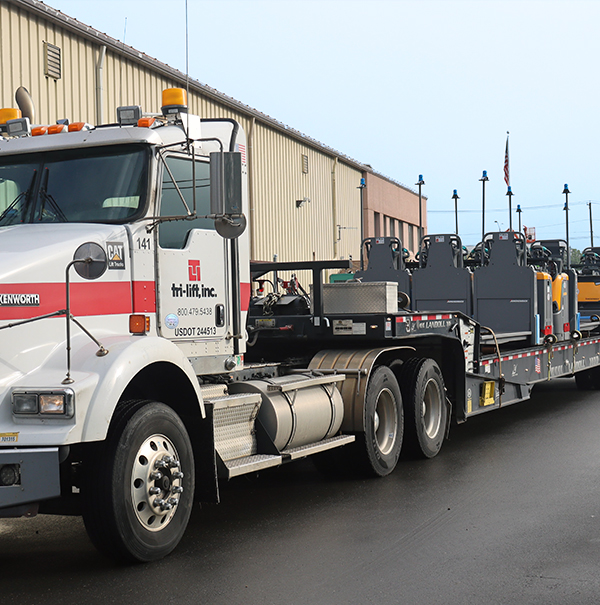
With nearly 900 late model aerial and forklift units available at our 5 strategically located facilities, Tri-Lift has one of the largest and most diverse selection of quality rental equipment in the region. In many cases we can deliver rentals with-in 24 hours. Our team of rental specialist can work with our customers to identify the right equipment for your project and make sure it is delivered when you need it.
Sometimes purchasing a forklift or aerial unit is not in the budget, Tri-Lift can help. We have equipment available to meet your business demand during your peak or seasonal times, when existing equipment is down or when physical inventories need to be performed, we are there for you. When it comes to aerial equipment, we have a vast array of equipment that can handle any task easily.
We Own & Operate 8 Delivery Trucks
Whether you are looking for short-term rentals or long-term rentals, we can provide you with the material handling and aerial equipment you need.
We pride ourselves on always delivering the right, reliable equipment to you on time at extremely competitive pricing.
Short Term Rentals
Renting a forklift or aerial for a day, week or month or yearly is as easy as a phone call or online request to our qualified forklift rental department. From one unit to an entire fleet.
We offer forklifts as small as 1,000 pounds and as large as 40,000 lbs or aerial booms and scissor lifts from 6 feet to a 120-foot lift. We offer many types:
- Brands: Cat, Mitsubishi, Jungheinrich, Linde, Genie, JLG, Kalmar and more.
- Sit-down three wheel and four-wheel electric units that can work inside and out (standup up counterbalance also available)
- Narrow aisle equipment (standup reaches, order selectors, turrets)
- Walkie, walkie rider, walkie stackers, tuggers and more
- Inside internal combustion forklifts
- Outside Pneumatic type forklifts
- Booms, Scissors, telehandlers, and work platforms readily available
- Fuel types available, Diesel, Propane and Electric
- A wide variety of forklift attachments to meet most applications
Long Term Rentals
As the business climate improves, you are likely to find yourself in need of material handling and aerial equipment. There are several options for acquiring usage on your fleet, and the decision you make today could dramatically impact your cash flow and bottom line. Long-term renting has been the choice for many companies, both large and small, for some time. We want to take a moment to point out just a few of the benefits that your company recognize by choosing a Long-Term Rental program from Tri-Lift.
- Customized terms up to 7 years
- Flexibility to upgrade equipment during the term
- No cash outlay
- Single paper rental contract (no third-party leasing involved) Flexible return policies
- No monthly parts and labor cost (ask for the details)
- Loaner equipment provided
- Tax-saving advantage
- Fleet reduction
- Competitive pricing
Call one of our specialists today to see how this program can change the way you manage your fleet. Call 800-479-5438, email
Tri-Lift Is Making Buying New Post Pandemic Easy As A,B,C
We Have Forklifts In Inventory and Rental Options To Get To Work Now
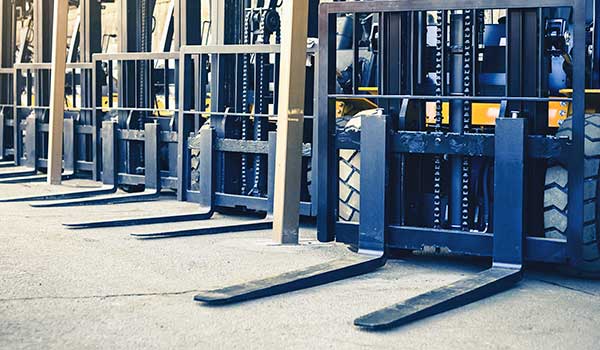
A - Buy New From Our Existing Inventory
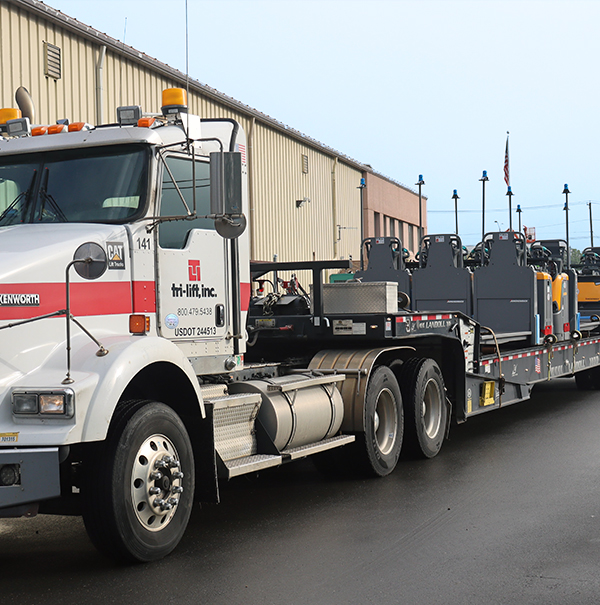
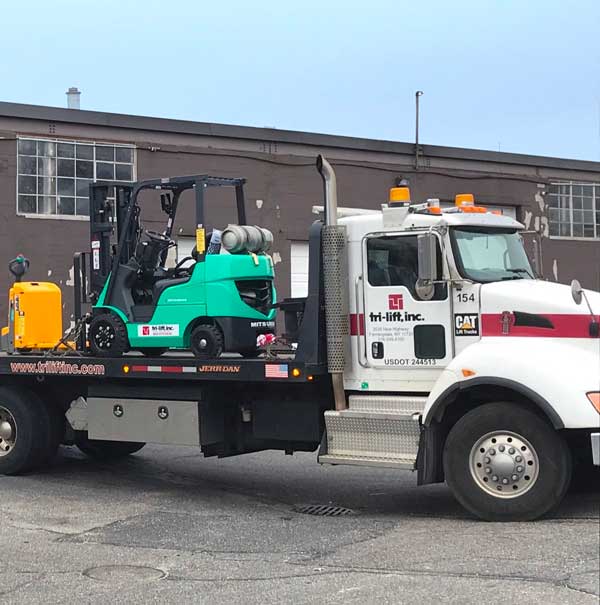
B - What you need is not in-stock? Select from one of these two rental options.
Option #1
Purchase a new forklift and Tri-lift will provide a monthly rental unit at our low published rate. When the invoice for the rental is paid in full, we will issue a credit worth 30% of the monthly rental cost back to your account. This credit can be used toward the sell price of the new unit when delivered or can be used as a credit toward any other services Tri-lift provides. Our rental units include all maintenance cost, so no additional charges need to be anticipated (misuse and damage are not included).
Option #2
Do not want to make any rash decisions on a purchase yet? Then why purchase a new unit if you cannot justify the need for one, or simply cannot endure the long lead times for delivery? Tri-lifts LTR (Long Term Rent) program offers the flexibility of a 1- or 2-year rental term at greatly reduced rates as a solution. Providing the ability to not make a rash decision while keeping your operation running at a favorable fee and with a limited term.
1 year “LTR” term: 30% discount off our current published rate.
2 year “LTR” term: 35% discount off our current published rate.
Once the “LTR” term has been completed and all payments have been made in full, Tri-Lift will provide an 5% rebate of the rental charges toward the purchase of a new truck, if the order of the new unit is given within 60 days of the end of the“LTR”term.
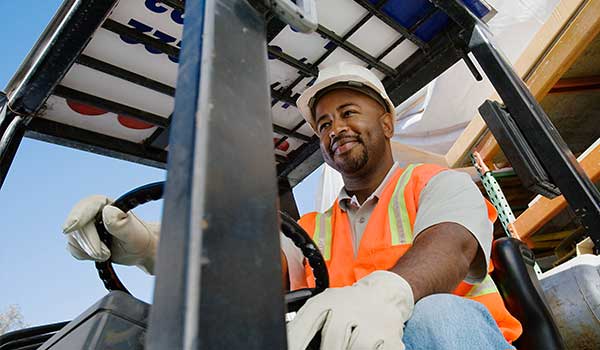
C - Get To Work
Put your forklift to work tackling your material handling application needs now - not at the convince of other manufacturers’ lead times. Contact Tri-Lift today!
Parts For All Forklift & Equipment Brands
In addition to providing replacement parts for all major OEM brands, Tri-Lift offers replacement parts for all brands of forklifts, material handling equipment and construction equipment.
We stock an array of new OEM parts for the Cat, Mitsubishi, Jungheinrich, Linde, Big Joe, Genie, JLG and Terex major brands which we are the authorized distributor for. In addition, we stock and inventory parts for all brands of equipment so when you need a part, you can rely on us. If we don’t have the part you’re looking for in stock, through our Promatch system we can find it for you. Our team is ready to help you keep your fleet running at full capacity. Let Tri-Lift be your single source for all of your parts no matter how diverse your needs be.
Order Parts 24/7 Online Parts Store
We stock parts for:
Cat
Mitsubishi
Jungheinrich
Linde
Baoli
Big Joe
Genie
Terex
SkyJack
JLG
Nissan
TCM
Unicarriers
Barrett
Toyota
Hyster
Yale
Raymond
Crown
Komatsu
Clark
Doosan
Daewoo
Kalmar
Heli
Hyundai
Halla
Powerboss
Tennant
Cushman
Moffet
Priceton
KD Manitou
And many more…
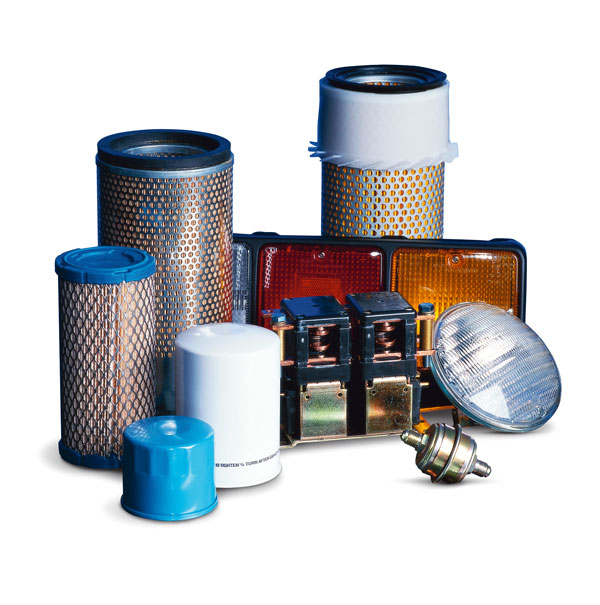
Online Parts Store (Join at No Cost)
- 24/7 ordering and access
- Search by part number
- Browse product catalogue
- View OEM manuals
- Convenient navigation and easy to use shopping cart
- Excellent website support and contact links on each page
- View complete part details and pictures
- Generate and manage quotes
- Search and view previous orders
- Multiple user access available
Parts Consignment
For larger fleets our on-site parts consignment program is a very flexible and cost-effective option for quickly replacing damaged or worn parts. We stock parts you commonly used at your facility, do the inventory, and you only pay for what you use - plain and simple. Now that is convenience!
If you have the part number you are looking for or need some help determining which part you may need, give us a call at 800-479-5438 or contact us online today.
Lithium Batteries
Upgrade your fleet today and experience the difference with our reliable lithium solution.
Lithium Advantages:
- Longevity – lead acid has a life span of 1,200 to 1,500 cycles and if you are opportunity charging this will greatly reduce its life. Lithium has a life span of 3,500 cycles and is built and designed to hand opportunity charging.
- Runtime – A lithium battery can run 3 shifts a day without the need for additional batteries, providing the process of opportunity charging is used.
- Maintenance Cost – Lithium does not need watering, cleaning, equalizing acid levels, and swapping out batteries.
- Energy Savings – Lithium batteries are 30% more efficient than a comparable lead acid battery and will result in lower electricity costs over time.
- Space Savings –With Lithium there is no need to have a separate area in the plant for charging forklift batteries because lithium does not gas when charging like a lead acid battery does. Thus, the company can recapture this area for more production or storage for the operation.
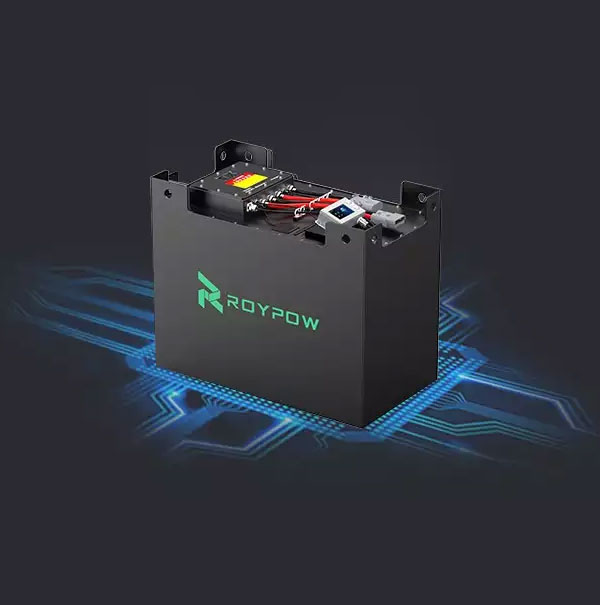
What Makes Tri-Lift’s Lithium Solution Different:
- Our Lithium battery is a LiFeP04 chemistry which does not contain nickel or cobalt in it. Both materials are rare and expensive and have environmental impacts and must be mined.
- Our lithium can run in greater operating temperature ranges.
- Our LiFePO4 lithium batteries have very high thermal and chemical stability. There are multiple built-in protections, including overcharging, over-discharging, overheating and short circuit protection. This makes our solution one of safest Lithium in the market.
- Optional way to acquire Lithium: Tri-Lift can finance a lithium package with a new truck purchase or if you want to upgrade an existing truck.
Request A Free Lithium Consultation & Quote
End-of-Year Forklift Blowout
Save BIG on the last remaining 2024 NEW FORKLIFT INVENTORY
Time is running out – the sale ends January 15th or while supplies last! Fill out the form below and secure your new forklift for 2025 operations.
*Quantities are limited. Prices do not include local delivery costs and taxes.
Additional Services
Budget Monthly Maintenance Program (BMM)
This program provides a flat monthly billing charge for all service and maintenance. Tri-Lift will perform an application survey to determine an estimated monthly cost to service customers equipment properly. This fee is estimated based on industry standards and customers environment and usage. Every quarter we will communicate to the customer the cost for the actual service performed. Compared to the Monthly budget payment. Any overage or underage differences are adjusted quarterly and either billed to customer or credit applied to customers account for future services needed. Term of the agreement is for a minimum of a year. Monthly payment maybe adjusted during the term with both parties’ consent. Does not calculate in the major repairs if needed.
Allows customer to budget monthly maintenance costs.
Total Maintenance & Repair Program (TM&R)
This program can include all repairs needed (parts & Labor) on existing fleet over a 1-to-3-year period based on age, hours, application, or condition. If program is used on a new unit, the program can be run from 1 year to 6 years customers choice. Customer will be billed monthly over the term decided. Customer has options to tailor program on what type of services they would like to include or exclude from the program.
This program is the best way to budget cost over the life of the unit.
Additional Services
- Emission testing done at customer facility with reporting on results
- Battery & Charger maintenance and watering.
- Battery evaluation and usage reporting
- Driver Safety operating training
- Complete Truck safety audit
- Tire replacement can be performed on site, at customer’s location
- Fleet Management Reporting on fleet utilization, cost per unit and repairs completed. All can be obtained in the cloud for immediate results.
- Dock & door maintenance programs
Let us create a service plan that works for you! Contact us at
Emergency Repairs: Help When You Need It
For emergency service, call 800.479.5438
Tri-Lift can help with emergency repair service when needed. We offer 24/7 access to service should your forklift or material handling equipment breakdown unexpectedly. Tri-Lift Inc. has the mobility to maintain and repair with the urgency you need and expect. Our technicians troubleshoot on the spot, with state of the art diagnostic tools. Technicians’ vehicles are always stocked, making them literally small, functional moving shops in themselves always equipped with the parts and tools needed to complete the service requirement.
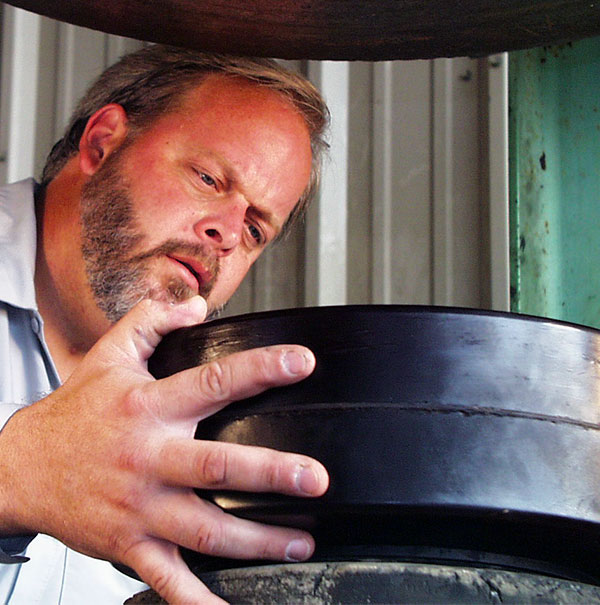
Tri-Lift's Time & Material (T&M) Program
This service provides the customer with full control over their maintenance on equipment. There is no commitment or agreement. Customer determines (we can assist) when they perform the planned maintenance or breakdown repair. Cost is billed on an hourly bases for either Planned maintenance service or emergency breakdown repair. A minimal travel cost will apply.
* This program is the most expensive way to maintain truck.
Let us create a service plan that works for you! Contact us at
Planned Maintenance: Offering Reliability & Efficiency For Your Fleet
Our PM programs are designed to prolong the life of your forklift and improving uptime.
Programs can be customized to meet your environment, safety protocol and application demands. Not all planned maintenance services are the same. We at Tri-Lift, Inc recognize that every customer is not the same and their needs are different, therefore we install flexibility to our service offerings.
Download Brochure Contact Us to Request a PM Program
PM Maintenance Program (PM)
This program, flat rates the labor portion of the service, which reduces the overall cost versus above plan. There is no travel expense for this service. An agreement is signed annually that will fix your cost on labor and will set a schedule of services need for the year agreed upon by customer. Agreement can be cancelled with 90-day notice.
This program is a cost effective way to keep your unit in peak operating condition, while making sure it remains safety compliant on a frequent period.
Managed PM Maintenance Program (MPM)
This program provides the same service as the (PM) program but will give the customer the ability to pay monthly for all parts and labor used for pm services. The monthly cost will reflect number of services needed in a year to keep unit in top peak condition. The cost for each service performed includes parts and labor, times the number of services per year divided by 12 to come up with monthly payment. No interest. This program allows customers to better budget their monthly maintenance expense and reduces the need for multiple po’s or checks.
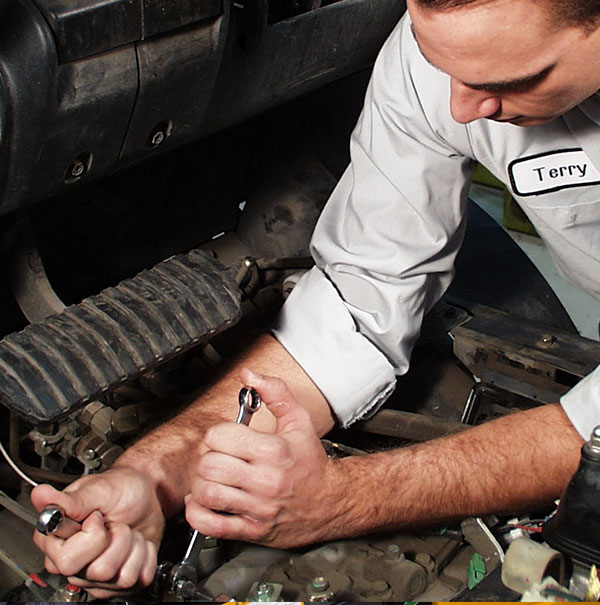
Planned Maintenance Benefits
A proper Planned Maintenance program can literally save thousands of dollars in maintenance costs over the life of a forklift or other material handling equipment. Factor in the added costs of lost productivity, calling for service and the scramble to get the job done during downtime, and your operating budget can get out of control.
- Aiding in the protection of equipment life
- Providing safety, operational and visual inspections
- Increasing uptime and productivity
- Reducing “emergency” downtime
- Increasing trade-in value
Let us create a service plan that works for you! Contact us at
Your Material Handling Fleet is the Heart of Your Business
Discover the best maintenance solutions for your lift truck and aerial fleet with one source.
Receive consistent services and pricing standards for all your locations, while being offered the latitude to determine the best type of maintenance program suited to your needs.
With Tri-lift’s comprehensive fleet service maintenance programs, our fleet service group will be able to determine the best solution for your business by evaluating your current lift trucks for annual usage, operating environment, application, and maintenance preference.
Tri-Lift Inc. is your answer for service. We are able to surpass the competition through our core of dedicated technicians, state-of-the-art technology, as well as multiple locations. Below are just a few of the ways we can support your fleet along with providing the flexibility needed in your operation and all at a competitive rate.
Tri-Lift Service Benefits
- Fully stocked vans ($12,500.00 worth of inventory)
- Fleet pricing on all parts provide
- (4) hour response time on emergency calls
- Factory Trained Service Technicians, with an average 60 hours training each year
- Fully insured
- A six-step audit process is performed before any invoice is sent to customer to verify accuracy and if unit or service is under warranty.